Л.И. Бондалетова
Промышленная экология
Учебное пособие / Том. политехн. ун-т. - Томск, 2002. - 168 с.
Глава 1. Производство и окружающая среда
1.3. Химико-технологическая система
1.3.2. Сырьевые ресурсы химико-технологической системы
Сырье является одним из основных элементов,
определяющих в значительной степени технологию производства, себестоимость и
качество продукта. Сырьем называют природные материалы, используемые в
производстве промышленных продуктов.
Исходными веществами для производства промышленных продуктов, кроме сырья, являются полупродукты
и вторичное сырье.
1.3.2.1. Характеристика и запасы сырья
Сырье химической промышленности классифицируют по
различным признакам:
– по происхождению ‑ минеральное, растительное и
животное;
– по химическому составу ‑ неорганическое и
органическое;
– по агрегатному состоянию ‑ твердое, жидкое
(нефть, рассолы) и газообразное (воздух, природный газ и газы
нефтепереработки);
– по запасам – возобновимое и невозобновимое.
Минеральное сырье делят на рудное (металлическое), нерудное и горючее (органическое).
Рудное минеральное
сырье, используемое для получения металлов в технически чистом виде, состоит из
природных минералов. Минералы руд содержат в основном оксиды и сульфиды
металлов (оксиды железа, сульфиды меди, цинка) и оксиды соединений,
составляющих пустую породу (оксиды кремния, алюминия, кальция, магния).
По составу минералов руды бывают окисленными ‑ состоящими
из оксидов, сульфидными и самородными.
Руды, в состав которых входят соединения разных
металлов, называют полиметаллическими.
Нерудное
минеральное сырье разнообразно по химическому составу и либо применяется в
естественном состоянии ‑ песок, глина, асбест, слюда и др., либо
поступает на химическую переработку ‑ сульфаты, фосфаты, карбонаты,
хлориды, алюмосиликаты и т. п.
Горючие
минеральные ископаемые ‑ торф, бурые и каменные угли, сланцы, а также
нефть и природный газ ‑ относят к органическим соединениям и используют в
качестве сырья и источников энергии.
Особенностью минерального сырья является его
невозобновляемость, а также неравномерность распределения по поверхности земли
и ее недрам.
Растительное и животное сырье ‑ древесина, хлопок, масла и жиры, молоко, кожа, шерсть
и т. п. ‑ перерабатывают или в продукты питания (пищевое сырье), или в
продукты бытового и промышленного назначения (техническое сырье). Источниками
растительного и животного сырья являются ресурсы естественной среды обитания:
земельные, лесные, водные. Многие виды растительного и животного сырья перед
поступлением в производство сортируют, перебирают и очищают. Коэффициент использования
растительного и животного сырья невелик, поэтому задача комплексного и максимального
использования этого сырья имеет еще большее значение, чем для минерального.
В химической промышленности широко применяются и такие
доступные и дешевые виды сырья, как вода и воздух.
Невозобновимое сырье не восстанавливается совсем или восстанавливается
значительно медленнее, чем идет его использование человеком в обозримый период
времени.
Возобновимое сырье – это растительное и животное, некоторое минеральное сырье (например,
соли, осаждающиеся в озерах). Темпы расхода этого вида сырья должны
соответствовать темпам его потребления, иначе оно станет невозобновимым.
Полупродукты
– вещества и материалы, являющиеся исходными в производстве продуктов и
полученные из природного сырья в другом производстве.
Вторичное сырье – используемые в производстве вещества и материалы, являющиеся
невостребованными в других производствах. Источниками их являются отходы
производства и отходы потребления.
Отходы производства ‑ это остатки, которые
получают при технологической переработке сырья, материалов или полуфабрикатов в
конечные продукты, они не соответствуют
требованиям, предъявляемым к готовой продукции, но после предварительной
обработки (или без нее) могут быть использованы в другом производстве в
качестве сырья.
Отходы потребления – бывшие в
употреблении вещества и изделия, восстановление которых экономически не
выгодно.
Стоимость сырья в химической промышленности составляет
в среднем 60-70 % себестоимости продукта. Решение сырьевой проблемы
осуществляется разнообразными путями: приближением источников сырья к производству,
т. е. использованием более дешевого местного сырья; переработкой отходов,
пылевых и газовых уносов основного производства в новые продукты, непосредственным
использованием отходов, предварительным обогащением сырья в целях повышения
концентрации полезных компонентов; заменой одного вида сырья другим, более
экономичным. Например, переход с каменного
угля как основного сырья химической промышленности на нефть и природный газ дал
большой экономический эффект. Расчетные данные свидетельствуют, что
себестоимость добычи и подготовки нефти в пересчете на единицу условного
топлива в 3,5 раза, а природного газа ‑ в 12 раз меньше, чем угля,
добытого шахтным способом. Дешевый и доступный природный газ и продукты
нефтепереработки обеспечивают снижение себестоимости продуктов массового
производства: пластических масс, синтетических волокон, каучуков, моющих
средств и др. Использование природного газа вместо кокса снижает почти вдвое
себестоимость аммиака и, соответственно, уменьшает себестоимость азотных
удобрений.
1.3.2.2. Принципы обогащения сырья
Важное технико-экономическое значение в рациональной
переработке сырья имеет использование концентрированного сырья, обогащенного полезными
компонентами. Применение концентрированного сырья снижает стоимость последующей
химической переработки и, следовательно, стоимость продукта производства и
повышает его качество. Такое сырье способствует интенсификации технологического
процесса и экономии топлива. Расходы на транспортировку сырья к месту
переработки снижаются пропорционально концентрации ценных компонентов.
Концентрированное сырье получают его обогащением.
В процессе обогащения отделяют ценные компоненты от примесей, используя
различия в их физических, физико-химических и химических свойствах, а также
разделяют на компоненты сложные смеси, полиметаллические руды. Методы обогащения
разнообразны и принципиально различны для твердого, жидкого и газообразного
сырья.
Твердое минеральное
сырье предварительно измельчают, далее измельченная масса поступает на
обогащение, в результате которого получают концентрат (фракция, обогащенная
полезными компонентами) и пустую породу ‑ хвосты. Для твердого сырья чаще
всего применяют механические способы обогащения ‑ рассеивание
(грохочение), гравитационное разделение, электромагнитную и электростатическую
сепарацию, а также физико - химический метод ‑ флотацию.
Рассеивание (грохочение) применяют для разделения твердой породы, содержащей
минералы различной прочности и образующей при измельчении зерна разной
величины. При последовательном пропускании измельченного сырья через грохоты ‑
металлические сита с отверстиями разных размеров ‑ происходит разделение
на фракции, обогащенные определенным минералом.
Гравитационное обогащение (мокрое и сухое) основано на разной скорости падения
частиц измельченного материала различной плотности и величины в потоке жидкости
или газа или на действии центробежной силы. Чаще всего проводят мокрое
обогащение в потоке воды. Центробежное ускорение в гидроциклонах во много раз
выше ускорения при осаждении частиц, поэтому они дают более высокую
производительность, чем осадительные камеры; соответственно меньше их габариты.
Гравитационные способы применяют для обогащения сырья в производствах
минеральных солей, силикатных материалов, в металлургии а также при обогащении
углей.
Электромагнитное и электростатическое обогащение основано на различиях в магнитной
проницаемости или в электрической проводимости компонентов сырья. Эти способы
применяют для отделения магнитовосприимчивых частей от немагнитных и
электропроводящих от диэлектриков.
Флотация ‑ широко распространенный способ обогащения, применяющийся для
разделения полиметаллических сульфидных руд, обогащения каменных углей и многих
других минералов. Флотация основана на различии в смачиваемости водой и
прилипании частиц обогащаемого минерала к пузырькам пропускаемого через пульпу
воздуха. Плотность агрегата минерал ‑ воздух меньше, чем плотность того
же объема пульпы, поэтому он всплывает на поверхность. Большинство минералов
природных руд мало отличаются по смачиваемости друг от друга. Для их разделения
необходимо создать условия неодинаковой смачиваемости водой отдельных
компонентов породы, для чего применяют разнообразные химические соединения ‑
флотационные реагенты.
Термическое обогащение
твердого сырья основано на различии в плавкости компонентов сырья. Например,
нагреванием серосодержащей породы отделяют легкоплавкую жидкую серу от пустой
породы, состоящей из более тугоплавких известняков, гипса и др.
Химическое
обогащение основано на различии во взаимодействии компонентов сырья с
химическими реагентами с последующим выделением образовавшегося соединения
осаждением, испарением, плавлением и т. п.
Для выделения ценных компонентов из жидкостей часто
применяют экстракцию ‑ избирательное растворение их в органических
растворителях. При последующей регенерации экстрагента выделяют одновременно и
поглощенные вещества.
Газовые смеси
разделяют, используя различия компонентов смеси в температурах кипения,
растворимости и других свойствах. Разные температуры кипения дают возможность
при сжатии и сильном охлаждении последовательно конденсировать отдельные
компоненты. Так, из коксового газа, содержащего 53-60 % Н2,
получают газообразный водород, последовательно конденсируя и отделяя
содержащиеся в газе углеводороды, оксид углерода, кислород и азот. В других
случаях газовую смесь сжижают и затем разделяют на компоненты перегонкой в
ректификационных колоннах.
Широкое распространение в промышленности для
разделения газовых смесей находят методы сорбции ‑ избирательное
поглощение компонентов смеси жидкими (абсорбция) или твердыми (адсорбция)
веществами. Поглощенные компоненты выделяют (процесс десорбции) нагреванием,
обработкой водяным паром и т. п.
1.3.2.3. Комплексное использование сырья
Сущность комплексного использования заключается
в последовательной переработке сырья сложного состава в ценные продукты для
наиболее полного использования всех компонентов сырья.
Примером комплексного использования органического
сырья является термическая переработка топлива ‑ угля, нефти, сланцев,
торфа. Так, при коксовании угля кроме целевого продукта ‑
металлургического кокса ‑ получают коксовый газ и смолу, переработкой
которых выделяют сотни ценных веществ: ароматические углеводороды, фенолы,
пиридин, аммиак, водород, этилен и др. Применение указанных веществ в качестве
продуктов народного хозяйства привело к снижению себестоимости кокса.
Комплексное использование сырья органически связано с наиболее
прогрессивной и экономичной формой организации химического производства ‑
комбинированием предприятий. Характерным примером комбинирования
является использование отходов основного производства для вновь организуемых
производств. Высокий экономический эффект подобной связи обусловлен
возможностью использования дешевого сырья ‑ отходов и совместным ведением
общезаводского хозяйства (централизованное подсобное обслуживание, транспорт,
складирование материалов и пр.). При этом сокращаются на 60-70 % капиталовложения
на общезаводское хозяйство, снижается себестоимость продукции.
Химическая промышленность и ее смежные отрасли наряду
с энергетикой и транспортом являются источниками загрязнения окружающей среды.
Борьба с загрязнением окружающей среды, в частности с промышленными выбросами, ‑
важнейшая проблема современности. Одним из главных приемов уменьшения, а иногда
исключения промышленных выбросов служит полное комплексное использование
всех компонентов химического сырья.
Достижения химии и химической технологии обеспечили
возможность замены пищевого сырья непищевым и растительного – минеральным
для производства технических и бытовых продуктов. Такая замена увеличивает
пищевые ресурсы народного потребления, сохраняет лесные богатства, снижает
себестоимость продуктов.
1.3.2.4. Воздух и вода как сырье химической
промышленности
Химическая промышленность использует воздух и воду в
огромных количествах и для самых разнообразных целей. Это объясняется
комплексом ценных свойств воздуха и воды, их доступностью и удобствами
применения.
Воздух в
химической промышленности применяют в основном как сырье или как реагент в
технологических процессах, а также для энергетических целей.
Технологическое применение воздуха обусловлено
химическим составом атмосферного воздуха;
сухой, чистый воздух содержит (объемная доля в %): N2 ‑ 78,10; О2 ‑ 20,93; Аr ‑ 0,93;
СО2 ~ 0,03 и незначительные количества Не, Nе, Кr,
Хе, Н2, СН4, О3, NО.
Чаще всего используют кислород воздуха в качестве окислителя:
окислительный обжиг сульфидных руд цветных металлов, серосодержащего сырья при
получении диоксида серы в сернокислотном, целлюлозно-бумажном производствах;
неполное окисление углеводородов при получении спиртов, альдегидов, кислот и
др. Кислород, выделяемый ректификацией жидкого воздуха, в больших количествах
расходуют для кислородной плавки металлов, в доменном процессе и т. п.; при
ректификации получают также азот и инертный газы, в основном аргон.
Азот используют в качестве сырья в производстве
синтетического аммиака и других азотсодержащих веществ и как инертный газ.
Воздух, применяемый в качестве реагента, подвергается, в зависимости от
характера производства, очистке от пыли, влаги и контактных ядов. Для этого
воздух пропускают через промывные башни с различными жидкими поглотителями (Н2О,
щелочи, этаноламины и др.), мокрые и сухие электрофильтры, аппараты с
влагопоглотительными сорбентами и пр.
Энергетическое применение воздуха связано, прежде всего, с использованием
кислорода как окислителя для получения тепловой энергии при сжигании различных
топлив.
Воздух используется также как хладоагент при
охлаждении газов и жидкостей через теплообменные поверхности холодильников или
в аппаратах прямого контакта (например, охлаждение воды в градирнях), при грануляции
расплавов некоторых соединений (например, аммиачной селитры). В других случаях
нагретый воздух используется как теплоноситель для нагрева газов или жидкостей.
В пневматических барботажных смесителях используют
сжатый воздух для перемешивания жидкостей и пульпы, в форсунках ‑ для
распыления жидкостей в реакторах и топках.
Вода
обладает универсальными свойствами, благодаря чему находит в народном хозяйстве
разнообразное применение как сырье, в качестве химического реагента, как
растворитель, тепло- и хладоноситель.
Например, из воды получают водород различными
способами, водяной пар в тепловой и атомной энергетике; вода служит реагентом в
производстве минеральных кислот, щелочей и оснований, в производстве
органических продуктов ‑ спиртов, уксусного альдегида, фенола и других
многочисленных реакциях гидратации и гидролиза. Водяной пар и горячая вода
имеют значительные преимущества перед другими теплоносителями ‑ высокую
теплоемкость, простоту регулирования температуры в зависимости от давления, высокую
термическую стойкость и пр., вследствие чего являются уникальными
теплоносителями при высоких температурах. Воду используют также как хладоагент
для отвода теплоты в экзотермических реакциях, для охлаждения атомных
реакторов, где необходима «сверхдистиллированная» вода.
Природные воды содержат различные примеси минерального
и органического происхождения. К минеральным примесям относятся газы N2, О2, СО2, Н2S, NН3,
растворенные в воде соли, кислоты и основания находятся в основном в
диссоциированном состоянии в виде катионов и анионов. К органическим примесям
относятся коллоидные частицы белковых веществ и гуминовых кислот. Состав и
количество примесей зависят главным образом от происхождения воды.
По происхождению различают атмосферные, поверхностные
и подземные воды.
Атмосферная вода ‑ вода дождевых и снеговых
осадков ‑ характеризуется небольшим содержанием примесей. В этой воде
содержатся в основном растворенные газы и почти полностью отсутствуют
растворенные соли.
Поверхностные воды ‑ воды речных, озерных и
морских водоемов ‑ отличаются разнообразным составом примесей ‑ газы,
соли, основания, кислоты. Наибольшим содержанием минеральных примесей
отличается морская вода (солесодержание более 10 г/кг).
Подземные воды ‑ воды артезианских скважин, колодцев, ключей, гейзеров
‑ характеризуются различным составом растворенных солей, который зависит
от состава и структуры почв и горных пород. В подземных водах обычно
отсутствуют примеси органического происхождения.
Качество воды определяется ее физическими и
химическими характеристиками, такими как прозрачность, цвет, запах,
температура, общее солесодержание, жесткость, окисляемость и реакция воды. Эти
характеристики показывают наличие или отсутствие тех или иных примесей.
Общее солесодержание характеризует присутствие в воде минеральных и органических примесей.
Для большинства производств основным качественным
показателем служит жесткость воды, обусловленная присутствием в воде
солей кальция и магния. Жесткость выражается в миллиграмм-эквивалентах ионов Са
или Мg в 1 кг воды, т. е. за единицу жесткости принимают
содержание 20,04 мг/кг ионов кальция или 12,16 мг/кг ионов магния.
Различают три вида жесткости: временную, постоянную и общую.
Временная
(карбонатная или устранимая) жесткость обусловлена присутствием в воде
гидрокарбонатов кальция и магния, которые при кипячении воды переходят в
нерастворимые средние или основные соли и выпадают в виде плотного осадка
(накипи):
Са(НСО3)2 = СаСО3 + Н2О +
СО2
2Мg(НСО3)2 = МgСО3 .
Мg(ОН)2 + ЗСО2 + Н2О
Постоянная
(некарбонатная, неустранимая) жесткость обусловливается содержанием в воде всех
других солей кальция и магния, остающихся при кипячении в растворенном
состоянии.
Сумма временной и постоянной жесткости называется общей
жесткостью. Принята следующая классификация природной воды по значению общей
жесткости (h в мг-экв/кг): h < 1,5 ‑ малая жесткость, h = 1,5-3,0
‑ средняя, h
= 3,0-6,0 ‑ повышенная, h
= 6,0-12,0 ‑ высокая, h
> 12,0 ‑ очень высокая.
Окисляемость
воды характеризуется наличием в воде органических примесей и выражается в
миллиграммах кислорода, расходуемого на окисление веществ, содержащихся в 1 кг
воды.
Активная реакция воды ‑ ее
кислотность или щелочность характеризуется концентрацией водородных ионов.
Реакция природных вод близка к нейтральной; рН ‑ водородный показатель,
равный (-lg aH+), колеблется
в пределах 6,8-7,3.
Производства в зависимости от целевого назначения воды
предъявляют строго определенные требования к ее качеству, к содержанию примесей
в ней; допустимые количества примесей регламентируются соответствующими
ГОСТами. Природная вода, поступающая в производство, подвергается очистке
различными методами в зависимости от характера примесей и требований,
предъявляемых к воде данным производством.
В промышленности в целях экономии расхода воды
применяют так называемую оборотную воду, т. е. использованную и возвращенную в
производственный цикл.
1.3.2.5. Промышленная водоподготовка
Промышленная водоподготовка представляет собой комплекс операций, обеспечивающих
очистку воды ‑ удаление из нее вредных примесей, находящихся в молекулярно - растворенном, коллоидном
и взвешенном состоянии.
Основные операции водоподготовки: очистка от
взвешенных примесей отстаиванием и фильтрованием; умягчение, а в
отдельных случаях – обессоливание; нейтрализация; дегазация и обеззараживание.
Отстаивание воды проводят в непрерывно действующих отстойных бетонированных
резервуарах. Для достижения полного осветления и обесцвечивания декантируемую
из отстойников воду подвергают коагуляции. Коагуляция ‑
высокоэффективный процесс разделения гетерогенных систем, в частности,
выделения из воды мельчайших глинистых частиц и белковых веществ.
Физико-химическая сущность этого процесса состоит в том, что адсорбция
коагулянта на поверхности заряженной коллоидной частицы приводит к слипанию
отдельных частиц (коагуляции) и образованию осадка. При этом ион-коагулянт
должен иметь заряд, противоположный заряду коллоидной частицы. Чем выше заряд
иона-коагулянта, тем меньше расход электролита на коагуляцию. Так, природные
глинистые коллоидные системы (природные воды) имеют отрицательный заряд, для их
коагуляции чаще всего применяют соединения алюминия в виде сульфатов или
двойных солей ‑ алюмокалиевых квасцов. Одновременно идет процесс
адсорбции на поверхности осадка органических красящих веществ, в результате
чего вода обесцвечивается. Количество вносимого в воду коагулянта находится в
прямой зависимости от загрязненности воды. Образующийся при коагуляции коллоидный
осадок удаляется из воды отстаиванием и фильтрованием.
Фильтрование ‑ наиболее универсальный метод разделения неоднородных систем. В технике
фильтрования большое значение имеет развитая поверхность фильтрующего
материала.
Умягчение и обессоливание воды состоит в удалении солей кальция, магния и других
металлов. В промышленности применяют различные методы умягчения, сущность
которых заключается в связывании ионов Са2+ и Мg2+ реагентами в нерастворимые и легко удаляемые
соединения.
По применяемым реагентам различают способы:
– известковый (гашеная известь);
– содовый (кальцинированная сода);
– натронный (гидроксид натрия) и
– фосфатный (тринатрийфосфат).
Процесс умягчения основывается на следующих реакциях:
1) обработке гашеной известью для устранения временной
жесткости удаления ионов железа и связывания СО2:
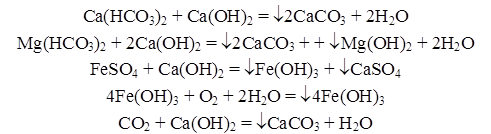
2) обработке
кальцинированной содой для устранения постоянной жесткости:
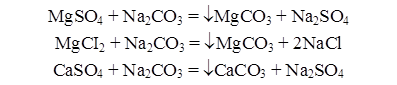
3) обработке
тринатрийфосфатом для более полного осаждения катионов Са2+ и Mg2+:

Растворимость фосфатов кальция и магния ничтожно мала,
это обеспечивает высокую эффективность фосфатного метода.
Наиболее
экономично применение комбинированного способа умягчения, обеспечивающего
устранение временной и постоянной жесткости, а также связывание СО2,
удаление ионов железа, коагулирование органических и других примесей. Одним из
таких способов является известково-содовый в сочетании с фосфатным.
Значительный
экономический эффект дает сочетание химического метода с физико-химическим,
т.е. ионообменным способом. Сущность ионообменного способа умягчения
состоит в удалении из воды ионов кальция и магния при помощи ионитов, способных
обменивать свои ионы на ионы, содержащиеся в воде.
Различают
процессы катионного и анионного обмена; соответственно иониты называют
катионитами и анионитами.
В основе катионного
процесса умягчения лежит реакция обмена ионов натрия и водорода катионитов на
ионы Са2+ и Mg2+:

Приведенные
реакции показывают, что ионообменный способ может обеспечить как умягчение
воды, так и обессоливание, т. е. полное удаление солей из воды.
Реакции
ионообмена обратимы, и для восстановления обменной способности ионитов проводят
процесс регенерации. Регенерацию
Na-катионитов осуществляют при помощи растворов поваренной соли,
а Н-катионитов ‑ введением растворов минеральных кислот. Уравнения регенерации
катионитов:

Примером анионного обмена может
служить реакция обмена анионов ОН- по уравнению

Регенерацию
анионита проводят при помощи растворов щелочей:

Полное обессоливание воды
может быть достигнуто также путем перегонки воды ‑ дистилляции ‑
на перегонных установках.
Повышение
технико-экономического эффекта водоподготовки связано с применением
комбинирования нескольких технологических процессов, например коагуляции,
умягчения и осветления с помощью современных методов ионного обмена, сорбции,
электрокоагуляции и др.
Для современной
промышленной водоподготовки значительный интерес представляет возможность
применения электрохимических методов, в частности электрокоагуляции.
Электрокоагуляция ‑ способ очистки воды в электролизерах с
растворимыми электродами ‑ основана на электрохимическом получении гидроксида
алюминия, обладающего высокой сорбционной способностью по отношению к вредным
примесям.
На растворимом алюминиевом аноде происходят два
процесса ‑ анодное и химическое (не связанное с протеканием
электрического тока) растворение алюминия с последующим образованием А1(ОН)3:

На катоде происходит выделение пузырьков газа ‑ водорода
(водородная деполяризация), поднимающих частицы веществ на поверхность воды. К
достоинствам метода электрокоагуляции относятся: высокая сорбционная
способность электрохимического А1(ОН)3, возможность механизации и автоматизации
процесса, малые габариты очистных сооружений.
Для очистки главным образом кислых оборотных вод
применяется нейтрализация ‑ обработка воды оксидом или гидроксидом
кальция.
Важной частью водоподготовки является удаление из воды
растворенных агрессивных газов (СО2, О2) с целью
уменьшения коррозии. Удаление газов осуществляют методом десорбции
(термической деаэрации) путем нагревания паром.
Воду, используемую для бытовых нужд, обязательно
подвергают обеззараживанию ‑ уничтожению болезнетворных бактерий и
окислению органических примесей в основном хлорированием при помощи
газообразного хлора, а также хлорной извести и гипохлората кальция.
1.3.2.6. Водообеспечение промышленных предприятий
Химические производства относятся к водоемким. Большую
часть воды расходуют для охлаждения и конденсации продуктовых потоков. В
значительной части технологических процессов воду используют как растворитель или вводят в виде пара. Воду применяют
и как реагент химических
реакций.
Основные пути улучшения водообеспечения
промышленных предприятий следующие:
-
разработка новых технологий,
характеризующихся сокращением потребляемой воды и образующихся загрязненных
стоков либо полным исключением воды из технологических операций;
-
создание локальных систем
обезвреживания стоков отдельных производств, включающих извлечение из них и
утилизацию ценных компонентов, подготовку очищенной воды к повторному
использованию;
-
организация замкнутых водооборотных систем, включая сбор и использование
очищенных сточных вод, паводковых вод и атмосферных осадков с территории
предприятий.
Существенное снижение водопотребления
достигается при замене водяного охлаждения воздушным. Действующими в отрасли
нормами технологического проектирования водяное
охлаждение допускается лишь в тех случаях, когда по каким-либо
причинам воздушное охлаждение невозможно. Аппараты воздушного охлаждения могут
быть использованы вместо градирен для отвода избыточного тепла воды. Градирни
открытого типа сложны в эксплуатации, в обычных условиях унос капельной влаги
из градирен достигает 0,3 % и более, при этом в районе градирен
загрязняются воздушный бассейн и почва. Особенно эффективны закрытые оборотные
системы с аппаратами воздушного охлаждения высокозастывающих
продуктов. Воздушное охлаждение позволяет сократить потребность в охлаждающей
воде на действующих предприятиях на 60-75 % и, следовательно, объем
сточных вод на 25-45 %. Соответственно снижаются потери сырья, основных и
побочных продуктов, уменьшаются капитальные затраты и эксплуатационные расходы
на водопотребление и водоотведение
(канализацию).
Водопотребление снижается также при замене
барометрических конденсаторов смешения (для создания вакуума) поверхностными
аппаратами. Расход охлаждающей воды при этом сокращается в 3-4 раза, экономится
энергия на перекачку воды, уменьшаются газовые выбросы в атмосферу.
Экономии воды способствует комбинирование процессов,
так как жесткие связи по сырью между блоками установок позволяют устранить промежуточное
охлаждение продуктовых потоков, а избыточное тепло на одном блоке утилизировать
на других.
Расход воды
снижается при повторно-последовательном использовании охлаждающей воды как на
отдельных технологических установках, так и на смежных установках и некоторых
объектах общезаводского хозяйства. Особенно эффективно оно в случае
предварительной стабилизации свежей и оборотной воды против выпадения и
разложения солей жесткости или специальной химической водоочистке свежей воды.
Воду при этом можно нагревать до более высоких температур, так как накипь на
трубах не образуется, а перед поступлением на градирню предварительно охлаждать
с утилизацией тепла для отопления помещений, теплиц или производства холода.
При такой схеме расход воды уменьшается в несколько раз.
С созданием крупных комплексов на нефтехимических
предприятиях сооружение локальных систем оборотного водоснабжения,
канализации и очистки сточных вод экономически выгодно. В этом случае снижаются
затраты на биологическую очистку сточных вод, улучшается контроль за их
качеством, сокращаются потери продуктов, уменьшается загрязненность окружающей
среды. Экономически целесообразна децентрализация оборотного водоснабжения на
действующих заводах с подключением к оборотным системам ограниченного числа
технологических установок. При рассредоточении оборотного водоснабжения и
уменьшении объема циркулирующей воды можно использовать герметизированные
напорные системы водооборота и канализации сточных
вод.
На ряде предприятий США и Западной Европы предусмотрены
раздельные системы канализации: ливневая, хозяйственно-фекальная, условно
чистая для ливневых вод и несколько производственных. Это позволяет
распределять сточные воды с учетом степени их загрязненности, качества и
свойств загрязнителей, выбирать наиболее оптимальные и дешевые методы очистки
для возвращения в оборотные системы. Некоторые типы вод, например слабощелочные
и слабокислые, целесообразно отводить в одну систему для их взаимной
нейтрализации и экономии реагентов.
Сточные воды, содержащие нефтепродукты, не следует
смешивать со сточными водами, содержащими вещества, способные образовывать
трудно разрушаемые эмульсии, стойкую пену или
увеличивать потери от испарения.
Оптимальное решение проблемы предотвращения
загрязнения водоемов и уменьшения дефицита воды ‑ создание
экономически рациональных замкнутых систем водного хозяйства предприятий.
Необходимость и целесообразность создания замкнутых систем производственного
водоснабжения обусловлены тремя основными факторами:
– дефицитом пресной воды. На увеличение дефицита
пресной воды влияют не только непрерывный рост водопотребления, но и деградация
качества воды природных водоисточников в результате поступления в них сточных
вод;
– исчерпанием обезвреживающей (самоочищающей и
разбавляющей) способности водоемов, в которые сбрасываются сточные воды;
– экономическими преимуществами по сравнению с
очисткой сточных вод до соответствующих нормативов, позволяющих их сброс в
открытые водоёмы.
Основные принципы создания
замкнутых водооборотных систем
Создание экономически обоснованных замкнутых систем
водного хозяйства является весьма трудной задачей. Сложный физико-химический
состав сточных вод, разнообразие содержащихся в них соединений и их взаимодействие
друг с другом делают невозможным подбор универсальной структуры бессточных
схем, пригодных для применения в различных отраслях народного хозяйства.
Вопросом первостепенной важности при создании
замкнутых водооборотных систем является разработка научно-обоснованных
требований к качеству воды, используемой во всех технологических процессах и операциях.
В подавляющем большинстве технологических операций
нет необходимости в использовании воды питьевого качества. Поэтому необходимо
оценить допустимые пределы основных показателей качества воды, которые определяются
следующими факторами:
– не должно ухудшаться качество получаемого продукта;
– должна обеспечиваться безаварийная работа
оборудования; оно не должно разрушаться вследствие коррозии, на стенках не
должны появляться отложения и т.д.;
– не влиять на здоровье обслуживающего персонала за
счёт изменения токсикологических или эпидемиологических характеристик воды.
Исторически сложилось так, что при разработке
технологических схем на качество воды не обращали внимания. Питьевая и даже
техническая вода в подавляющем большинстве случаев удовлетворяла технологов, а
использованную воду просто сбрасывали в водоёмы и только позднее стали направлять
на очистные сооружения.
Общими задачами при разработке замкнутых водооборотных
систем для всех отраслей народного хозяйства являются следующие:
– максимальное внедрение воздушного охлаждения вместо
водяного: на многих предприятиях на охлаждение расходуется до 70 % всей
используемой воды;
– размещение комплекса производств на промышленной
площадке таким образом, чтобы было возможно многократно (каскадно) использовать
воду в технологических производствах;
– последовательное многократное
использование воды в различных или идентичных производствах должно приводить к
образованию небольшого объема максимально загрязненных сточных вод, для
обезвреживания которых можно подобрать достаточно эффективные (и, как правило,
дорогостоящие) методы очистки;
– использование воды для очистки газов только тогда,
когда из газов извлекаются и используются ценные компоненты, применение воды
для очистки газов от твердых частиц допускается только в случае замкнутого
цикла;
– обязательная регенерация отработанных кислот,
щелочей и солевых технологических растворов с использованием извлекаемых
продуктов в качестве вторичного сырья.
При создании замкнутых водооборотных систем
промышленных предприятий водоподготовка и очистка сточных вод должны
рассматриваться как единая система. Проектирование замкнутых систем проводится
одновременно с проектированием основного производства.
Схемы водообеспечения промышленных
предприятий
При
прямоточном водообеспечении вся забираемая из
водоема вода после использования в технологическом процессе возвращается в
водоем за исключением безвозвратных потерь в производстве и потерь со шламом на
очистных сооружениях (рис. 8,а).
Схема повторного использования сточных вод после их
очистки показана на рис. 8,б. Незагрязненные нагретые сточные воды поступают на
охладительные установки (градирни, охладительные пруды), а затем возвращаются в
оборотную систему водообеспечения. Загрязненные
сточные воды поступают на очистные сооружения. После очистки часть отработанных
сточных вод подают в систему оборотного водообеспечения, если их состав удовлетворяет нормативным требованиям.
Исходя из существующего технического уровня отраслей,
повторно используется 92-98 % воды. В отдельных производствах этот
показатель достиг 100 %, т.е. воду используют многократно без сброса
загрязненных стоков в водоемы, а свежую воду добавляют в связи с естественной
убылью (испарение, химическое превращение и др.). Так, на предприятиях
нефтеперерабатывающей и нефтехимической промышленности оборотные системы обеспечивают
91 % производственных потребностей в воде.
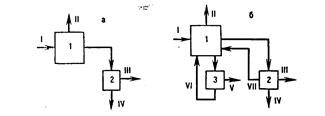
Рис. 8.
Схемы водообеспечения промышленных предприятий:
а - прямоточная; б – оборотная; 1 – предприятие;
2 – очистные сооружения:
3 - охладительные установки; I ‑
вода из источника; II ‑ безвозвратные потери воды; III
‑ вода, удаляемая со шламом; IV ‑
вода, сбрасываемая в водоем;
V ‑ потери воды на испарение и унос; VI
‑ оборотная вода после охладительных установок; VII ‑ то
же после очистных сооружений
Однако переход от частичных оборотных систем к
полностью замкнутым оборотным системам связан не только с дополнительными
капитальными затратами на строительство соответствующих очистных сооружений, но
и с решением двух основных задач: устранением минерализации и покрытием потерь
оборотной воды
При
циркуляции в системе часть воды испаряется в градирнях, с поверхности открытых
прудов и очистных сооружений, при удалении шламов и осадков, теряется в результате
участия в химических реакциях, подвергается различным физико-химическим
воздействиям, в том числе упариванию, в результате
чего в ней увеличивается концентрация солей и накипеобразующих
соединений. При многократном использовании в воде накапливаются механические
взвеси, различные коррозионно-агрессивные соединения и микроорганизмы. Все это
вызывает интенсивное отложение накипи и коррозию оборудования, ухудшает
теплопередачу. Из-за увеличения содержания в воде
солей и других примесей требуется вывод части воды и замена ее свежей. С этой
целью осуществляют так называемую подпитку, или продувку системы. Взамен
сброшенной из водоема забирают свежую воду. Покрыть потери оборотной воды можно
за счет бытовых сточных вод, а также дождевых и паводковых вод после
предварительной их подготовки.
При организации оборотного водообеспечения
предусматривают методы борьбы с карбонатными отложениями, биологическими
обрастаниями, коррозией оборудования, а также методы подготовки подпиточной воды.
Накапливающиеся в оборотной воде соли образуют на теплообменной поверхности так называемые карбонатные
отложения, более чем на 50 % состоящие из карбоната кальция. Основные
методы снижения отложений:
1) обработка охлаждающей воды кислотой (обычно серной)
для снижения общей щелочности воды;
2) фосфатирование путем введения в воду раствора гексаметафосфата натрия, тормозящего процессы
кристаллизации и осаждения карбоната натрия на стенках аппаратуры;
3) обработка воды магнитным полем, что вызывает
быстрый рост кристаллов карбонатных и других отложений, которые сорбируют на
своей поверхности ионы карбонатов кальция и магния, растут и выпадают в виде
шлама, легко уносимого потоком.
При оборотном водоснабжении возникает проблема борьбы
с биологическими обрастаниями. Разнообразные живые существа (бактерии),
проникая из открытых водоемов в систему оборотного
водоснабжения, поселяются на любой твердой поверхности, соприкасающейся с
водой, развиваются, образуют поселения, называемые биологическими обрастаниями;
сами организмы называются биогентами. Допустимой считается скорость развития
биологических обрастаний теплообменных аппаратов и трубопроводов в оборотной
воде не выше 0,07 г/(м2-ч), т.е. в течение месяца толщина нарастающего
слоя должна быть не более 0,05 мм. Для борьбы с бактериальными биогентами
применяют хлор, а для уничтожения водорослей ‑ медный купорос. Дозы и
периодичность хлорирования определяют на основе лабораторных исследований
оборотной воды. Водоросли развиваются в основном в теплый период года. Поэтому
купоросом обрабатывают воду 3-4 раза в месяц в период с апреля по октябрь.
Содержащиеся в оборотной воде соли и другие примеси
вызывают коррозию оборудования. Хлориды ускоряют коррозию вследствие
увеличения кислотности воды и их разрушающего действия на пассивирующие пленки; сульфаты агрессивно действуют на
бетон. Диоксид углерода замедляет образование защитных пленок. Для защиты от
коррозии в оборотных системах применяют различные ингибиторы. Процесс коррозии
приостанавливают хромат и бихромат калия. Они же замедляют биологические обрастания.
Для снижения коррозии воду обрабатывают также фосфатами, которые образуют
пленку, изолирующую металл от воды. В отличие от хроматов фосфаты
благоприятствуют развитию биологических обрастаний, поэтому эти химикаты иногда
применяют совместно. Один из способов защиты металла от коррозии ‑
защитные покрытия смолами, красками, лаками и эмалями, однако они недолговечны
и восстановить их можно только во время ремонта.
Для предотвращения и удаления карбонатных отложений и
биологических обрастаний систему оборотного водообеспечения систематически очищают
механическим способом, гидропневматической промывкой или с помощью химических
реагентов.
Таким образом, полностью замкнутая система
водообеспечения предполагает постоянный количественный и качественный состав
воды, предотвращение коррозии оборудования, загрязнения системы как
минеральными, так и биологическими отложениями, отсутствие сброса загрязненных
вод в водоемы, ликвидацию сбросов другими способами.
|